Eliminated Hand Deburring
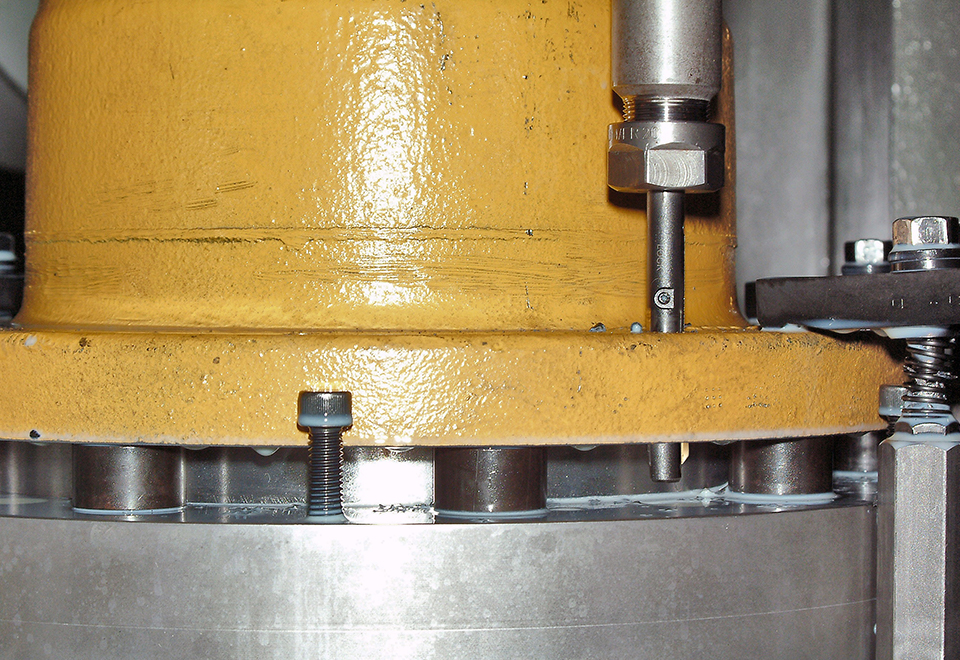
Application
An extremely large Earth moving machine hub, about 3x the size of a standard automotive part.
Material
Nodular iron
Tool
Customized carbide for larger holes, and a standard carbide for standard holes
The Challenge
The nodular iron component at 80lbs is an 11.6 inch hub with 22 holes, 10 @ .425 diameter and 12 @ 1.093. The challenge was how to deburr the backside of this large hub in a productive manner.
Skyway was removing the 80lb hub and placing it on a workbench to manually deburr the holes using a countersinking tool in an air drill. This required further man-hours, and man-power. Plus the countersink tool was expensive with a short tool life.
The Solution
We designed a special 9” long tool to work at 550 RPM @ 8.8 IPM (1.087 hole).
For the smaller holes, a standard length carbide tool at 1750 RPM @ 11 IPM (.425 hole). Both carbide tools gave Skyway the ability to deburr the backside of the hole efficiently while the hub remained in the machine.
The Results
The E-Z Burr carbide tools eliminated the process to remove the hub from the machine to hand deburr the rear of the holes. This not only saved Skyway 20 minutes per part but also alleviated the frustration within workers and potential health hazards and risks.
The countersinking tool Skyway was using to hand deburr the back of the hub would last a day or two, whereas E-Z Burr’s carbide insert would run a month before the need of replacement. The tool itself remained in the machine while the insert was being replaced.